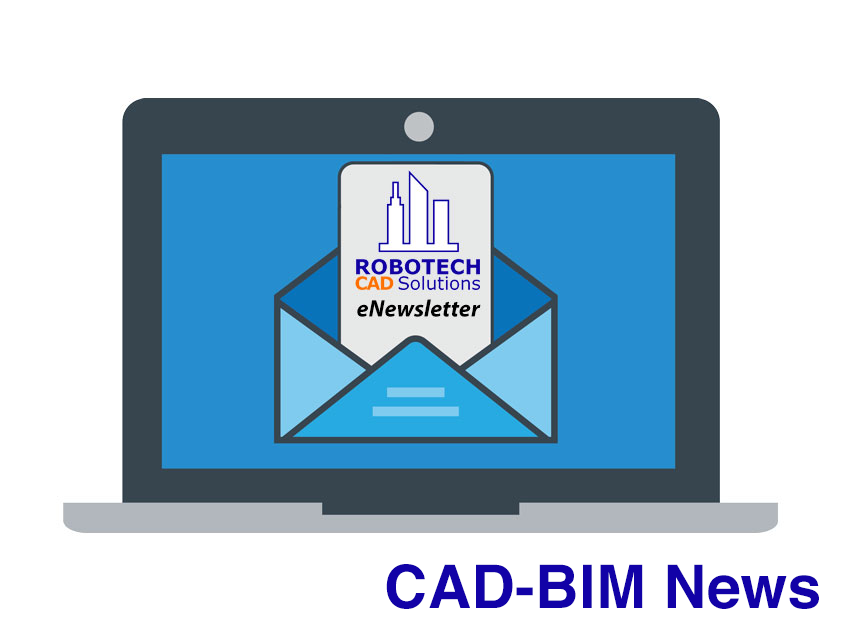
AutoNews BIM Monthly Newsletter – March 2025
AutoNews is an informational newsletter, courtesy for Robotech’s customers and followers. We hope you enjoy it and we welcome your feedback.
AutoNews is an informational newsletter, courtesy for Robotech’s customers and followers. We hope you enjoy it and we welcome your feedback.
The architecture, engineering, and construction (AEC) industry has undergone a seismic shift over the past few decades, driven by the evolution of technology from Computer-Aided Design (CAD) to Building Information Modeling (BIM). This transformation has not only revolutionized how buildings are designed and constructed but has also redefined collaboration, efficiency, and sustainability in the industry. From the early days of 2D drafting to the sophisticated 3D modeling and data-rich environments of today, the journey from CAD to BIM is a testament to the power of innovation in shaping the future of construction.
1960s: The Birth of CAD
The story begins in the 1960s, when the first CAD systems emerged. These early tools, such as Sketchpad developed by Ivan Sutherland, allowed designers to create digital 2D drawings. While revolutionary at the time, these systems were limited in scope and required significant computational power, which was expensive and inaccessible to most.
1980s: The Rise of 2D CAD
By the 1980s, CAD software became more accessible and widely adopted. Programs like AutoCAD, introduced by Autodesk in 1982, enabled architects and engineers to create precise 2D drawings more efficiently than manual drafting. This era marked the beginning of the digital transformation in the AEC industry, as firms began to transition from paper-based workflows to digital ones.
1990s: The Emergence of 3D Modeling
The 1990s saw the introduction of 3D modeling capabilities in CAD software. Tools like Autodesk’s 3D Studio and Bentley Systems’ MicroStation allowed designers to create three-dimensional representations of buildings. While this was a significant step forward, these early 3D models were primarily visual and lacked the data-rich features that define modern BIM.
2000s: The Dawn of BIM
The concept of BIM began to take shape in the early 2000s. Unlike traditional CAD, BIM is not just about creating drawings or models; it’s about creating a digital representation of a building that includes both geometric and non-geometric data. Autodesk Revit, launched in 2000, was one of the first BIM platforms to gain widespread adoption. Revit allowed architects, engineers, and contractors to collaborate on a shared model, integrating design, construction, and operational data into a single platform.
2010s: BIM Goes Mainstream
The 2010s marked the mainstream adoption of BIM across the AEC industry. Governments and organizations worldwide began mandating BIM for public projects, recognizing its potential to improve efficiency, reduce errors, and enhance collaboration. During this time, Autodesk Revit continued to evolve, adding features like parametric modeling, cloud collaboration, and integration with other tools such as Navisworks for clash detection and analysis.
2020s: BIM and Beyond
Today, BIM is no longer just a tool but a foundational element of the AEC workflow. The integration of BIM with emerging technologies like artificial intelligence (AI), virtual reality (VR), and the Internet of Things (IoT) is pushing the boundaries of what’s possible. For example, AI-powered tools can now analyze BIM data to optimize building performance, while VR allows stakeholders to visualize and interact with BIM models in immersive environments.
BIM has become indispensable to the AEC industry, transforming how projects are planned, designed, constructed, and managed. Unlike traditional CAD, which focuses primarily on geometry, BIM provides a holistic approach by embedding critical data into every component of a building model. This data-driven methodology enables better decision-making, reduces errors, and improves collaboration among stakeholders.
One of the standout BIM platforms in the industry is Autodesk Revit. Revit’s robust features, such as parametric modeling, real-time collaboration, and interoperability with other software, make it an ideal choice for architects, engineers, and contractors. Its ability to create detailed, data-rich models ensures that all project stakeholders are working from the same information, minimizing misunderstandings and rework. Furthermore, Revit’s integration with Autodesk’s ecosystem, including tools like BIM 360 for cloud-based collaboration, enhances its utility in modern construction projects.
The evolution from CAD to BIM represents more than just a technological shift; it signifies a fundamental change in how the AEC industry approaches building design and construction. BIM’s ability to integrate data, improve collaboration, and enhance efficiency has made it an essential tool for modern construction projects. As the industry continues to embrace digital transformation, platforms like Autodesk Revit will play a pivotal role in shaping the future of construction, enabling smarter, more sustainable, and more innovative buildings. The journey from CAD to BIM is far from over, and the possibilities for what comes next are as exciting as the progress we’ve already made.
In a rapidly changing world, Gen Z has emerged as a driving force for a greener and more sustainable future. Unlike previous generations, Gen Z (born between 1997 and 2012) has grown up with increasing awareness of environmental issues and the visible impacts of climate change. With their unique perspectives and a deep sense of urgency, this generation is not only advocating for sustainability but also actively shaping how businesses, governments, and communities approach environmental challenges. The influence of Gen Z on sustainability is profound, and it is only growing stronger.
One of the key reasons Gen Z is more focused on sustainability is that they have grown up witnessing the effects of climate change firsthand. From severe weather events to shrinking biodiversity, this generation has seen how unsustainable practices have harmed the planet. For Gen Z, the climate crisis isn’t a distant threat; it’s a present reality. This has fostered a heightened level of environmental awareness and responsibility. Unlike their predecessors, who may have treated environmental issues as a secondary concern, Gen Z considers sustainability a core value, influencing everything from their consumption habits to career choices.
Gen Z’s preference for sustainable products and brands is reshaping markets across the globe. Research shows that this generation is willing to pay a premium for eco-friendly options and expects transparency from companies regarding their sustainability practices. According to a survey highlighted by Autodesk, nearly 75% of Gen Z respondents stated they would prefer to buy from sustainable brands even if it costs more. Their demand for ethical, environmentally friendly products is pushing businesses to adopt green practices, rethink their supply chains, and reduce their carbon footprints. Companies that ignore this shift risk losing a significant share of this influential consumer base.
Digital natives by nature, Gen Z is using technology as a powerful tool in their fight for sustainability. They are leveraging social media platforms to raise awareness, advocate for change, and hold corporations accountable. Additionally, this generation is embracing innovations such as renewable energy, sustainable design, and the circular economy. Tools like AI-driven software, green building solutions, and eco-friendly product design, as discussed in Autodesk’s article, are becoming popular among young creators who are determined to make a positive impact. Gen Z’s tech-savvy approach is accelerating the adoption of sustainable practices and encouraging the development of cutting-edge solutions for environmental challenges.
Beyond influencing consumer behavior, Gen Z is also making waves in the political sphere by advocating for systemic changes that support sustainability. They are vocal about the need for comprehensive environmental policies and regulations, from reducing single-use plastics to advancing renewable energy initiatives. This generation has a strong presence in grassroots movements, climate strikes, and advocacy groups, using their collective voice to push for government action on climate issues. By prioritizing long-term sustainability over short-term profits, Gen Z is helping to steer policy discussions towards a more sustainable future.
Gen Z’s vision of success goes beyond personal wealth and career achievements; it’s rooted in creating a positive and lasting impact on the world. This generation is redefining what it means to be successful by emphasizing social and environmental responsibility. They are more likely to pursue careers in green industries, support businesses that prioritize sustainability, and engage in activism to address climate change. As a result, their values are setting new standards for companies and policymakers, urging them to prioritize sustainable development. Gen Z’s commitment to sustainability is a powerful force that promises to reshape our world for the better, making it greener, more equitable, and more resilient.
The future of sustainability looks promising with Gen Z at the forefront. Their passion, technological proficiency, and collective action are paving the way for a more sustainable world, inspiring individuals, businesses, and governments to adopt greener practices. As this generation continues to rise in influence, their impact on the planet will likely be one of the defining legacies of our time.
For companies today, a driving force behind increasing sustainability practices is Gen Z—those born between the late 1990s and early 2010s—both as a workforce and as consumers. This generation is deeply concerned about the negative impacts of climate change, taking action in their own lives and pushing their employers to do the same. Gen Z currently makes up 27% of the global workforce. That share is expected to grow to 31% by 2035 and will have a massive influence on the future of sustainability initiatives in the workplace.
According to Autodesk’s 2024 State of Design & Make report, 97% of organizations are already taking steps to improve sustainability—a five-point increase over 2023—showing the issue has become a priority for most companies.
The State of Design & Make report is based on surveys and interviews conducted by Autodesk with almost 5,400 leaders, futurists, and experts from the architecture, engineering, construction, and operations (AECO); design and manufacturing (D&M); and media and entertainment (M&E) industries from countries around the world.
Sustainability initiatives across these industries include using artificial intelligence (AI) to optimize decision-making during the conceptual design phase, increasing the use of recycled materials and renewable energy, investing more in energy-efficient processes and equipment, and making efforts to reduce waste.
Although sustainability is good for the planet, companies’ embrace of this approach stems, in part, from a growing realization that it is also good for the bottom line: 69% of leaders and experts say sustainability is beneficial for businesses over the short-term, with 87% saying the same for long-term success, according to the report.
For example, sustainability efforts can decrease operating costs by reducing material and energy use. They can also improve organizations’ reputations with customers and employees—many of whom now see sustainability as essential for any business.
“Regardless of [people’s] age, climate change poses a significant existential threat around the globe, and we must work as a global community to make meaningful change,” says Hafsa Burt, founder and studio head of California-based hb+a Architects. “This needs to start with accountability.”
Forces are converging that motivate companies to move toward greater sustainability, with more than four out of five State of Design & Make respondents saying they face pressure from government regulators, customers, employees, and investors to be more sustainable. Currently, 36% of leaders and experts say employees are “very influential” in encouraging them to create and meet sustainability goals, up from 23% last year.
Although the impacts of climate change will be felt most strongly by younger generations, no single age group is responsible for driving sustainability initiatives across industries. “We have a lot of people who have been active in this space through choices, advocacy, policymaking, and practice for decades,” Burt says.
However, “Gen Z has more awareness [of sustainability] because of access to information and data,” she says. As a result, the influence of employees on sustainability efforts extends to younger generations, with the State of Design & Make report showing similar rates across industries:
AECO industry: About one-third of respondents say the next generation is “very influential” in encouraging their companies to become more sustainable, with the highest rate (41%) among the mining, oil, and gas sectors.
D&M industry: The percentage of leaders and experts who say the next generation is “very influential” in driving sustainability initiatives ranged from 29% in the building products and fabrication sector to 40% in the industrial machinery sector.
M&E industry: More than four in 10 respondents in the film, TV, and games sectors say the next generation is “very influential” in motivating their companies’ sustainability efforts, with a lower rate (32%) in the advertising, publishing, and graphic design sectors.
Climate change impacts everyone, but research suggests that it weighs especially heavily on the minds of younger generations. According to Deloitte Global’s 2024 Gen Z and Millennial Survey, climate change is a major concern for younger generations, with six in 10 Gen Zs saying that they felt worried or anxious about climate change in the past month.
Many are channeling their worries into positive actions—the report found that 73% of Gen Zs say they are taking steps to minimize their own impact on the environment, such as avoiding buying fast fashion, eating a vegetarian or vegan diet, or reducing air travel.
They are also pushing for change in the workplace. According to the survey, 54% of Gen Zs report pressuring their employers to take action on climate change. Slightly more agree that their employers are working to address climate change, though they believe more progress is needed.
Although these findings fit with what leaders and experts in the AECO, D&M, and M&E industries are seeing, younger employees may not feel their actions are having much impact, and they are willing to change jobs or even industries as a result. According to Deloitte Global’s survey, 20% of Gen Zs have changed jobs or industries because of environmental concerns, and another 26% plan to do so in the future. When changing roles, 72% of Gen Zs say a potential employer’s environmental credentials and policies are important considerations.
These trends suggest that organizations need to improve how they communicate to employees and job applicants about their strategies for minimizing the impacts of climate change. “There is an expectation of transparency and openness, and employers need to openly communicate their goals and progress toward sustainability,” Burt says. “There is a strong need to prioritize social responsibility benefiting local and global communities, as well as transparency about ethical labor practices throughout a company’s supply chains.”
On April 15, 2019, a wave of emotion swept the world as flames engulfed the iconic Notre-Dame Cathedral in Paris. But with this tragedy, came the promise to rebuild.
Images of the fire sparked an outpouring of global support and Autodesk knew right away we would join in, starting with a cash donation. Thanks to the initiative of our CEO Andrew Anagnost, we also offered our expertise in 3D digital modeling.
A core group of Autodesk employees was quickly formed to support the French public institution Rebâtir Notre-Dame de Paris throughout the restoration. Autodesk also partnered with Art Graphique & Patrimoine (AGP), a leading French company in laser scanning and digitization of historic monuments.
Out of this partnership, a highly detailed digital model of Notre-Dame was created by combining existing scans with new laser surveys. This BIM model, along with Autodesk software, was provided free of charge to the public institution Rebâtir Notre-Dame and made available to construction site stakeholders via a technology and skills patronage agreement.
Five years after a devastating fire, Notre-Dame de Paris is opening her doors once again, on December 7th and 8th, 2024. Autodesk honors the countless architects, artisans, engineers, and builders who worked tirelessly to bring Notre-Dame de Paris back to life.
With the growth of the urban population, apartment management companies in New York City face increasing pressure to provide both environmentally sustainable and community-focused accommodation.
In this article, we will explore emerging trends of green, sustainable, and community-focused housing that are reshaping NYC’s apartment scene.
Photo by Daryan Shamkhali on Unsplash
Rigorous green building certifications such as Leadership in Energy and Environmental Design (LEED) have become the benchmark in New York City as developers embrace ecological design. LEED rates buildings on factors like energy use and water efficiency.
Another fast-growing certification is Germany’s Passive House standard. This focuses strictly on reducing energy consumption through high-performance insulation and ventilation. Top projects pursuing these elite certifications include The Visionaire and East Harlem’s Sendero Verde.
As global warming accelerates, the boom of green-rated apartments in New York City sparks hope that high-density populations can coexist responsibly with the planet.
The straight answer to this question would be ‘pretty good’. As environmental standards tighten, NYC apartment landlords are racing to implement eco-friendly features. As a matter of fact, the state of New York ranked 5th in the nation for the most buildings with LEED certification, according to a report that came out in 2020.
New York City plays a huge role in that, with more than 40% of the residential buildings in the city now holding LEED green certifications. In addition, thousands more units tout Energy Star appliances, LED lighting as well as low-flow plumbing.
NYC buildings are racing to integrate solar power into residential buildings for clean energy and long-term savings. Top projects include The Brighton in Brooklyn, which has rooftop photovoltaic panels that provide emissions-free electricity. Some even go beyond solar, leveraging geothermal energy for heating and cooling needs.
The sleek solar panels showcase sustainability and protection from electricity cost hikes. But the most important aspect is that these buildings serve as models for profitable real estate that supports larger zero-emission goals.
Although NYC has gained the title concrete jungle, buildings across NYC are incorporating nature by adding sustainable features such as living rooftop gardens.
There are several benefits to rooftop gardens. For example, the rooftop oasis at 515 West 29th absorbs stormwater, cools the surrounding air, and nurtures wildlife. Besides these benefits, the rooftop gardens function as insulation, shrinking energy bills by reducing heating and cooling demand.
With the acceleration of climate change, rooftop gardens not only have critical environmental benefits but also bring unexpected beauty to this crowded concrete jungle. Finally, vibrant rooftop gardens spark hope that urban living can coexist with nature across global metropolises.
Beyond simply adopting renewable technologies, New York’s green developers also employ recycled and responsibly sourced construction materials that curb ecological harm from sourcing and manufacturing. In addition, the organic textures also blend sustainability and aesthetics by using natural warmth in sleek minimalist designs.
As tenants increasingly seek sustainability, these eco-friendly materials also boost property value. In addition, reusing materials helps New York City take tangible steps toward a waste-free, eco-friendly urban living.
Forward-looking apartment managers now integrate eco-friendly amenities, thus redefining modern rental lifestyles. Beyond gyms, communities entice conscious residents by offering electric car charging stations, curbside recycling pickup, and even on-site urban farms.
In addition, community gardens serve as a good way to connect the people and planet. These communal green spaces allow urbanites to reconnect with nature and neighbors either by yielding pesticide-free produce or simply nourishing the soul.
As climate consciousness grows among new generations, the purpose of such amenities can’t be overlooked as they serve to add value to people’s lives. This is done by fulfilling yearnings for belonging and environmental impact. Ultimately, even small habit shifts scaling holistic sustainability signal promising trends toward greener city living.
Smart home technologies promote urban sustainability by optimizing performance through connectivity and automation. Landlords across the market deploy self-learning thermostats and LED lighting gadgets that respond to natural daylight and low-flow water fixtures.
Examples include flagship properties like The XI in Chelsea that interface these IoT devices into elaborate efficiency platforms like Lutron HomeWorks for granular lighting and shade control. By providing tenants with insights into their consumption, these smart systems reduce energy use.
As the technologies get cheaper, incorporating smart features into your home could help curb emissions even with more people living in New York City. Apartment management companies are racing to implement many types of smart building technology. Examples of smart building technology range from simple devices that regulate the temperature to more complex devices that can control even security.
In conclusion, as climate change accelerates alongside urban growth, New York City apartment management companies face escalating pressure to adopt sustainable building practices.
Fortunately, the city’s most innovative property management companies are rising to meet these modern challenges. Landlords across New York City are pioneering super-efficient and community-connected housing by incorporating renewable technologies, ecological materials, and smart automation.
With precedents ranging from LEED-certified towers to passive solar complexes blooming with rooftop gardens, New York real estate boldly blazes trails to harmonize high-density populations and the planet.