ARCHIBUS & AUTODESK SOLUTIONS PROVIDER
Robotech is a Software & Services Provider for CAD, BIM and CAFM applications Message UsHelping you maintain and improve your CAD, BIM or CAFM operations
We offer Autodesk software & services for design automation, and Archibus IWMS suite of products for Corporate Facility Management. Robotech offers full implementation, training and support services for CAD, BIM and IWMS implementation.
Facilities Management
We offer our clients, corporate, real estate, education, healthcare and government institutions, high quality services and support with the best possible performance from our professional staff
CAD & BIM Software
For over 30 years we have been and Autodesk Reseller, implementing Autodesk Design Solutions for Architecure, Engineering and Construction professionals
CAD & BIM Training
Robotech has been training our clients in cutting-edge Autodesk CAD and BIM software for over 30 years as an Authorized Autodesk Training and Certification Center
Making you successful and profitable with
Autodesk & Archibus technology
Over 30 years in Workplace
Design and Facilities Management
“I highly recommend Robotech FM Solutions for consultation on the licensing, implementation and development of facilities management applications. Robotech has also developed and maintained custom applicaitons in Archibus that enable NYULH to track and optimize space utilization in its research portfolio through key performance metrics used by peer institutions.”
“It has been a pleasure working with the Robotech team since 2009. I can not say enough about the professionalism, quality, and service Shlomo and his team provides with our Archibus projects. Upon purchasing the Archibus/AutoCAD products they have worked with our IT Unit on the specifications and installation, provided training on several occasions, have customized databases or fields based on our needs, performed a smooth transition to the Web based version and are always available for questions and technical support.
“Robotech FM Solutions has been integral to my organization for over 20 years. They have provided Archibus and Autcad development, maintenance and design services for over 8 million Square Feet of space. Their teams are highly specialized and continue to exceed all of our expectations ”
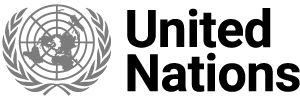
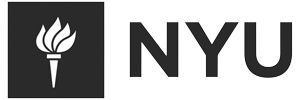
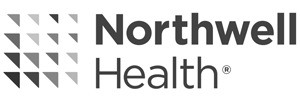
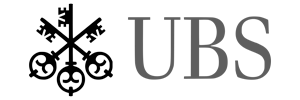